Hot Melt Yarn
As our main product, polyester cone dyed yarn is that undergoes high-temperature and high-pressure dyeing processing in a tube dyeing machine. This dyeing process allows the polyester yarn to maintain its excellent performance while achieving efficient and environmentally friendly dyeing production. Compared to dope dyed polyester yarn(uses color masterbatch for dyeing), polyester cone dyed yarn has higher quality.
Application:Shoes upper / Collar&Rib
Parameters
Name | Hot melt yarn / Low melting yarn |
Material | 100 percent polyester yarn / 100 percent nylon yarn |
Type | Filament yarn |
Technic | Spinning |
Denier | 50D,75D,100D,150D,200D customizable |
Melting point – 100% polyester | Initial melting point 110-140°C |
Melting point – 100% nylon | 90°C-110°C |
Luster | Semi-dull,customizable |
Feature | Strong adhesive capability, rapid curing, environmentally friendly, and good strength and durability |
Product
Production workshop
Video Introduction
Key Word
- low melting yarn
- hot melt glue yarn
- thermofuse hot melt yarn
Feature
The advantages of YM THREAD ‘s Hot Melt Yarn
Our Company hot melt yarn is a type of textile material commonly used in the production of various textile products, such as flyknit shoe uppers, fabrics, and bonded threads. Its distinctive feature is its low melting point, allowing it to melt at relatively low temperatures and then solidify upon cooling, forming fibers or threads.”
- Excellent bonding performance: Hot Melt Yarn exhibits outstanding bonding capabilities, which can be used to bond different parts of textiles together, thereby enhancing the strength and durability of textiles. It provides a stronger and more secure bond compared to traditional sewing or adhesive bonding, making it less prone to separation.
- Efficient production process: The application of Hot Melt Yarn can improve production efficiency. It can be easily applied to textiles through automated equipment, eliminating the need for labor-intensive manual sewing.
- Good wash resistance: It remains bonded and maintains its adhesive properties even after multiple washes. It can effectively retain its appearance and performance.
- Lightweight design: Hot Melt Yarn can be used to manufacture lightweight textiles as it does not add significant weight. It provides a balance of softness and strength, making it suitable for lightweight textile production.
- Applicability to various materials: Hot Melt Yarn can be applied to a variety of textile materials, including cotton, polyester, nylon, silk, and more. Its versatility makes it suitable for manufacturing different types of textiles.
- Environmentally friendly: Hot Melt Yarn typically does not require the use of harmful organic solvents or chemicals, contributing to a reduction in environmental pollution. Additionally, due to its efficient application and wash resistance, textiles made with Hot Melt Yarn are more durable, reducing waste generation.
Application
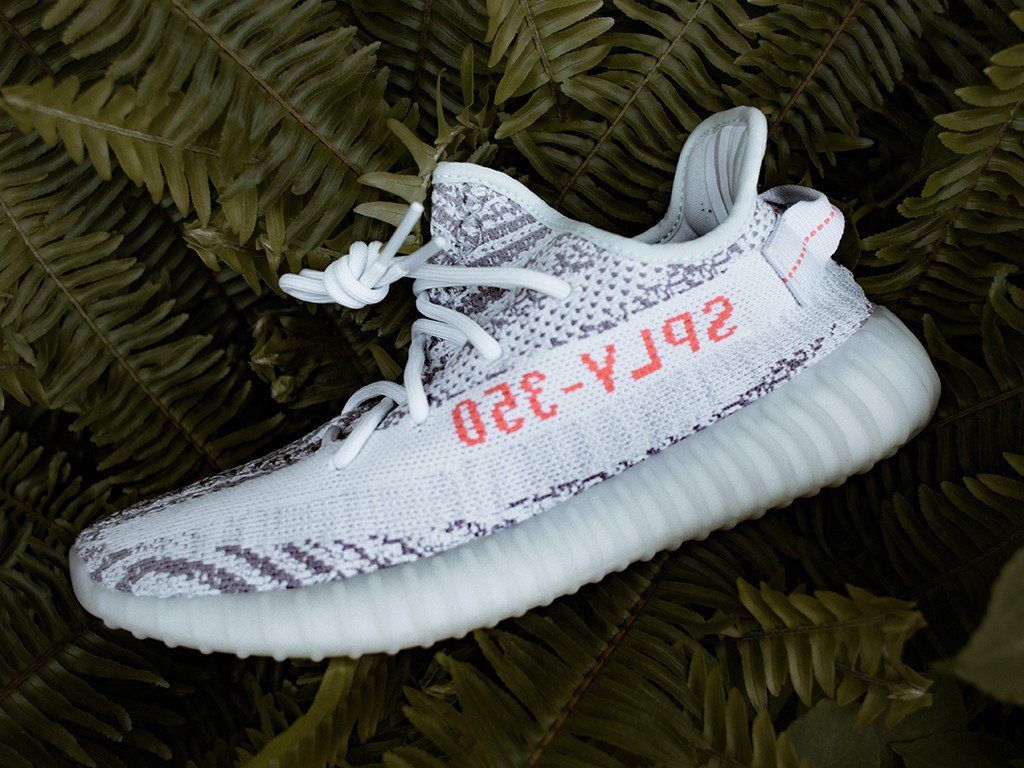
Flyknit Shoes Upper
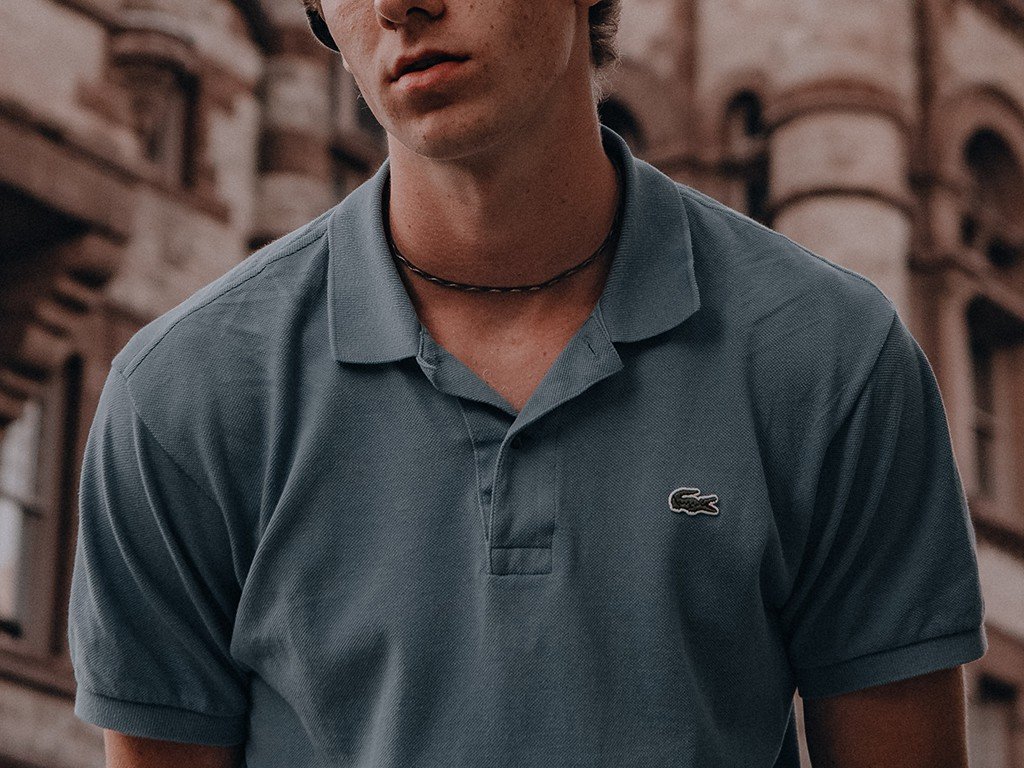
Collar
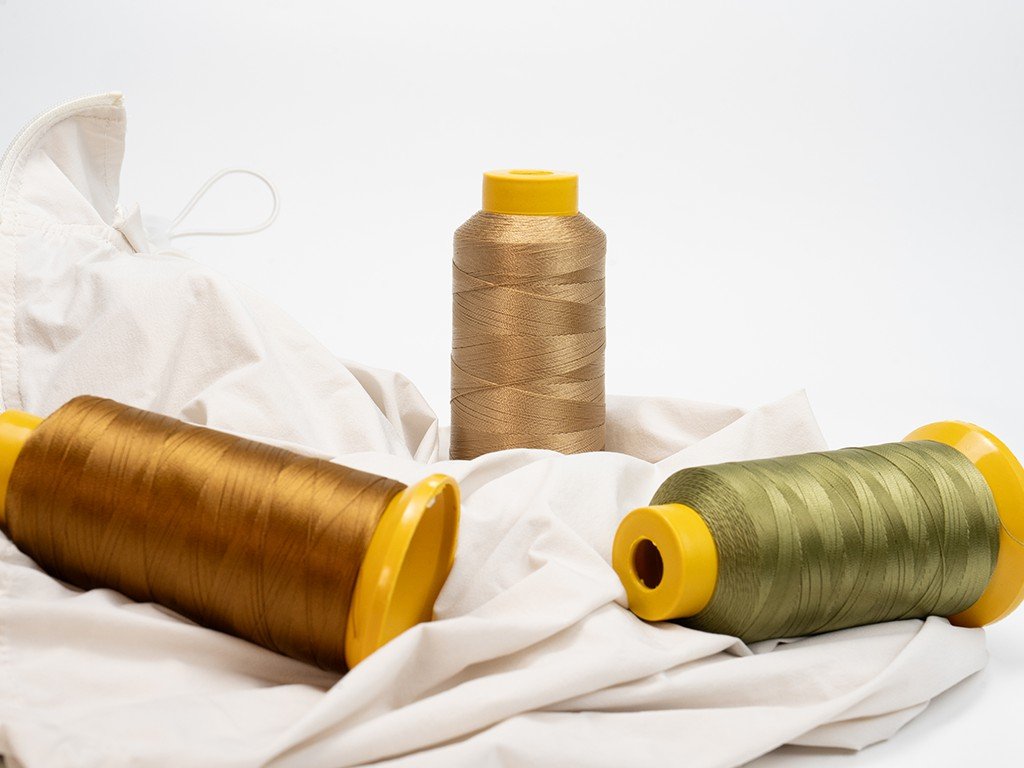
bonded thread
More about hot melt yarn
What is melting yarn?
“Hot Melt Yarn(low melting yarn) is a special type of textile material with unique properties and applications. Here is a detailed explanation of Hot Melt Yarn:
- Material Composition: Hot Melt Yarn is typically made from synthetic polymers such as polyester, polypropylene, and others. These polymers have lower melting points, allowing them to melt at relatively low temperatures and then solidify upon cooling, forming fibers or threads. The choice of material depends on specific application requirements.
- Adhesive Performance: The primary characteristic of Hot Melt Yarn is its exceptional adhesive performance. When heated, Hot Melt Yarn can quickly melt and bond to the surface or different parts of textiles, creating a strong connection. This bonding is often more robust than traditional sewing or adhesive bonding, making it widely used in the production and manufacturing of textiles.”
How to produce hot melt yarn?
In summary, the production process of polyester hot melt yarn involves key steps such as raw material preparation, melting and extrusion, cooling and solidification, cutting and packaging. Precise process control and quality management are crucial to ensuring the performance and quality of the final product.
Process | Process Description | Machinery/Equipment |
1. Raw Material Preparation | – Prepare polyester resin pellets and additives (such as color dyes, antioxidants). – Mix and blend the raw materials. | Raw material storage equipment, mixing machine, stirrer. |
2. Melting and Extrusion | – Heat the blended raw materials, polyester resin, to above its melting point. – Extrude the molten resin into fine filaments. | Extrusion machine (Extruder), heating units, screw extruders, filters. |
3. Cooling and Solidification | – Cool the extruded filaments using cooling airflow or a water cooling system. – Optionally, use a stretching machine to adjust filament strength and elasticity. | Cooling fans, water cooling system, stretching machine. |
4. Cutting and Packaging | – Use an automatic cutting machine to cut the long filaments into the desired lengths. – Package the cut filaments into rolls for storage and transportation. | Automatic cutting machine, packaging equipment, winding equipment. |
5. Quality Control | – Conduct rigorous quality inspections and testing, including diameter measurement, tensile strength testing, color consistency checks, etc. | Inspection equipment, testing instruments (e.g., tensile testing machine, diameter measurement device). |
6. Application Areas | – Apply polyester hot melt yarn in various textile applications, such as fabric production, sewing thread manufacturing, and footwear materials. | Textile production equipment (e.g., weaving machines, sewing machines, footwear production equipment). |