Parameters
Name | Polyester spun yarn |
Type | Spun yarn |
Material | 100 percent polyester yarn |
Technic | ring spun |
Denier | 10s 16s 20s 24s 30s 32s 40s 50s 60s customizable |
Luster | Semi-dull,customizable |
Feature | Good color-fastness,less feather,uniform texture,soft feeling,low shrinkage rate and high abrasion resistance. |
Product
Product
Video Introduction
Key Word
- sock yarn
- soft spun yarn
- polyester ring spun yarn
Feature
The advantages of YM THREAD ‘s Polyester Spun Yarn
- Structural Stability: Polyester spun yarn has tightly arranged fibers, ensuring a stable yarn structure. This structure not only provides excellent mechanical properties but also maintains the overall shape of the fabric.
- Abrasion Resistance: Polyester staple fibers are highly abrasion-resistant, making yarn and fabrics made from them more durable during long-term use.
- Chemical Stability: Polyester exhibits strong chemical stability and resistance to acids, alkalis, and organic solvents. This makes polyester spun yarn suitable for various chemical treatment processes, ensuring good stability.
- Low Moisture Absorption: Polyester fibers have low moisture absorption, meaning that polyester spun yarn dries quickly.
- Ease of Processing and Dyeing: Polyester spun yarn is easy to process, and its fibers have good dye absorption properties, allowing the production of vibrant and long-lasting textiles.
- Cost-Effective: Compared to many other fibers, polyester has lower production costs, making polyester spun yarn an economically efficient choice.
- Versatility: Polyester spun yarn can be blended with other natural or synthetic fibers, creating different textile qualities to meet diverse market demands.
Application
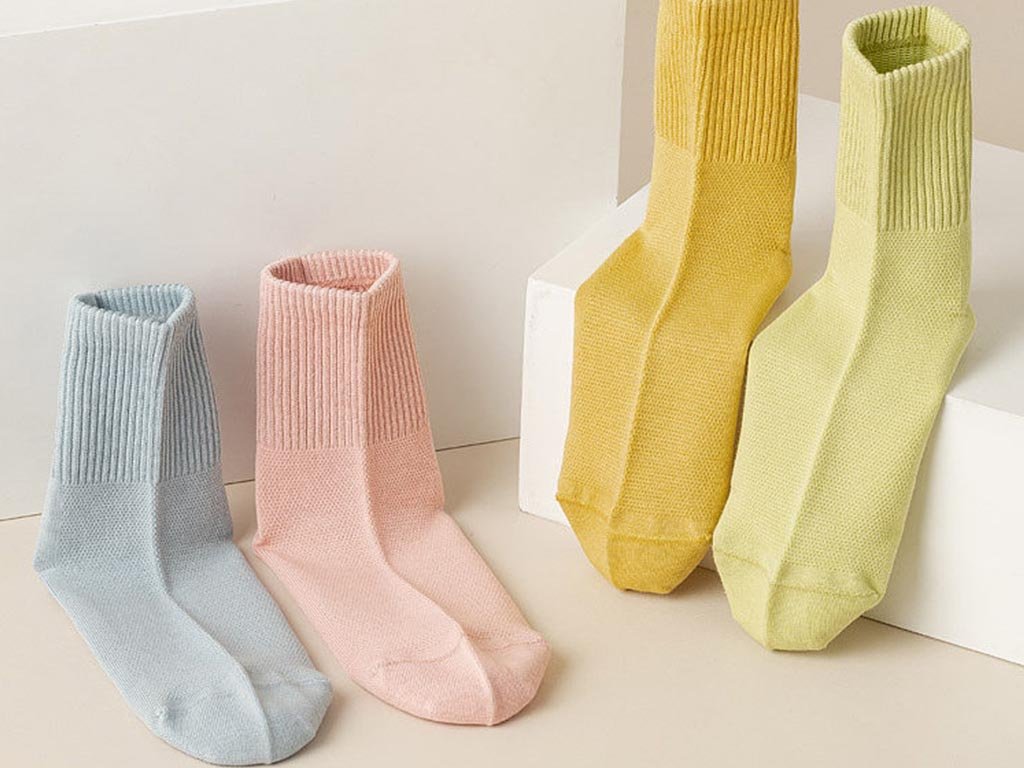
Socks
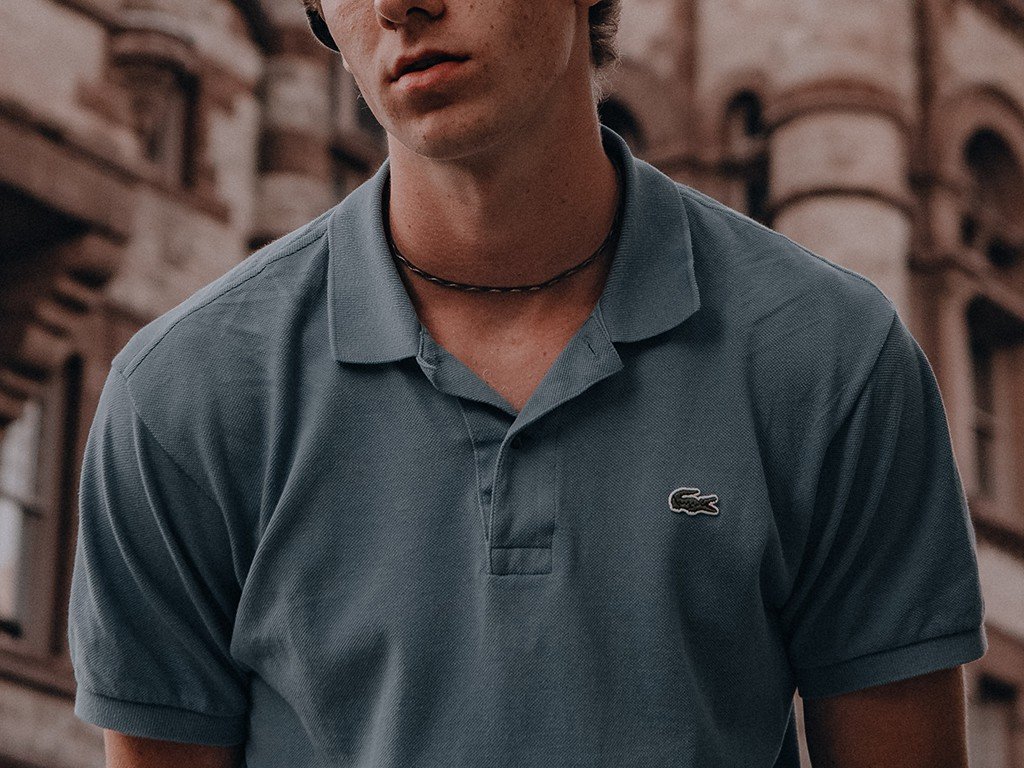
Collar

Shoeslace
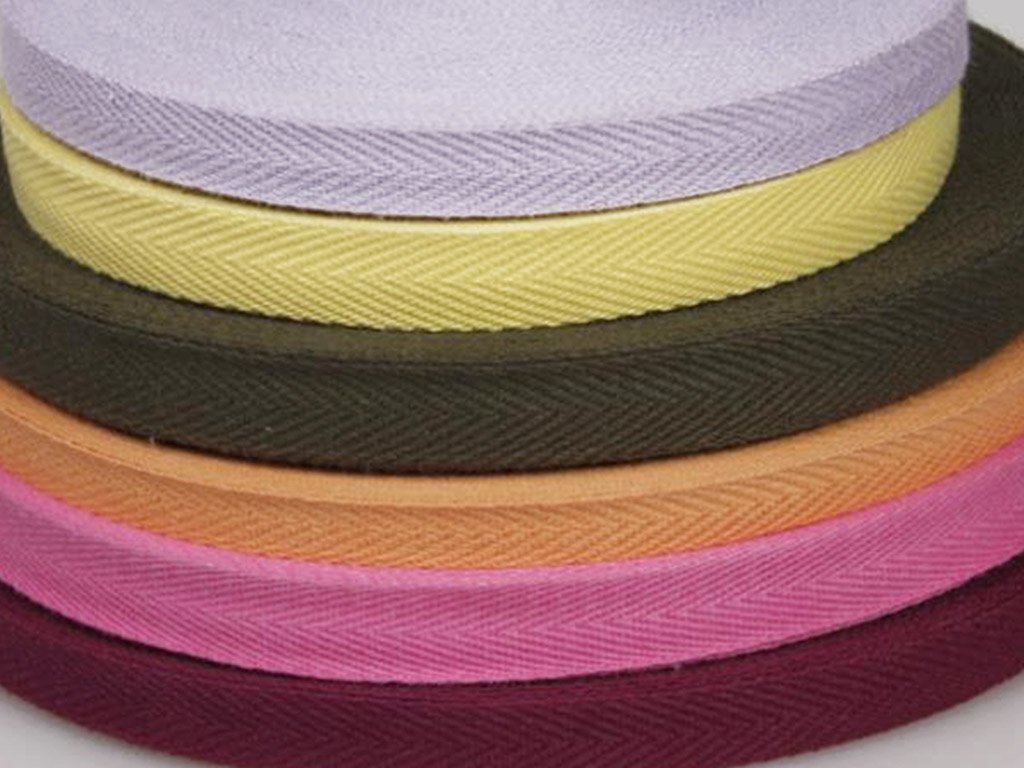
Webbing
Color Card
More about Spun Yarn
What is spun yarn and filament yarn?
Spun Yarn and Filament Yarn are two main types of yarn
- Spun Yarn: Spun Yarn is made from short fibers or fiber bundles. In the process of making spun yarn, fibers are typically first carded and straightened before being spun into yarn. This process involves firmly twisting the fibers together to form yarn. Spun yarn is often softer than filament yarn because it is composed of many short fibers intertwined, making it suitable for soft textiles such as socks,T-shirts, jeans, and bedding. Spun yarns typically have some fine fuzz or fiber ends on their surface, adding to their texture.
- Filament Yarn: Filament Yarn is made from continuous long fiber bundles, which are usually very long and uninterrupted. This type of yarn is usually more uniform and smooth, without fine fuzz or fiber impurities. Filament yarn is commonly used to produce smooth, glossy fabrics like silk, nylon, and polyester. Due to its continuous fiber structure, filament yarn has a more consistent appearance and is suitable for textiles requiring high uniformity and surface shine.
How is polyester spun yarn produced?
1.Spinning: Spinning is the core step in manufacturing yarn and typically includes the following sub-processes:
- Melting: Heating the preprocessed polyester pellets to their melting point, transforming them into a liquid state.
- Extrusion: Passing the molten polyester through an extrusion machine to create a molten stream.
- Cooling and Solidification: Cooling the molten polyester stream rapidly through cooling equipment, causing it to solidify into long filaments.
- Drawing: Stretching the filaments through a series of drafting rollers or air jet devices to increase their strength and improve fiber alignment.
2.Fiber Blending and Coloring (Optional): In some cases, different colors or types of polyester fibers may be blended together to achieve the desired color or performance characteristics. This typically occurs in special processes during spinning.
3.Yarn Quality Inspection: To ensure quality and compliance with specifications, quality control and inspections are carried out during the spinning process. This may include checking parameters such as yarn count, strength, fineness, uniformity, and appearance.
4.Winding: The spun polyester yarn is wound onto bobbins or cones for storage and transportation. These bobbins often have specific yarn lengths and packaging specifications.
5.Dyeing and Finishing (Optional): Depending on requirements, the polyester yarn may undergo dyeing in a dyeing facility to achieve the desired colors. Subsequently, it may require finishing processes to make the yarn smoother, softer, and more uniform.
6.Packaging: Finally, dyed or undyed spun polyester yarn is packaged into cones or spindles, ready for shipment to textile mills or other manufacturing facilities for use in making various fabrics and textile products.”